In high angle or extended reach wells, Torque is generally not a good indicator of hole condition – in most cases torque friction factors actually REDUCE over the course of a long drilling section. In the example below, a 6000ft section of high angle 9⁷⁄₈” hole was drilled. Right after drilling out the previous casing shoe surface torque was 4k ft-lb and equivalent to a 0.50 friction factor. Looking ahead to TD, if the friction factor stayed the same, torque would have been nearly 20k ft-lb. Even more concerning, with that friction factor rotation of the 7” liner string would have been impossible. But as drilling progressed, the torque friction factor was continuously reducing. Two factors drive this very common phenomenon: 1) while rotating at high speed (for hole cleaning) the tool-joints are polishing the inside of the previous casing creating a lower friction surface and 2) as a cutting bed develops the drill pipe is supported by the cuttings and the hard, oil coated cuttings act effectively as ball bearings. It’s always important to monitor torque in any complex well – but don’t expect it to tell you if the hole is clean!
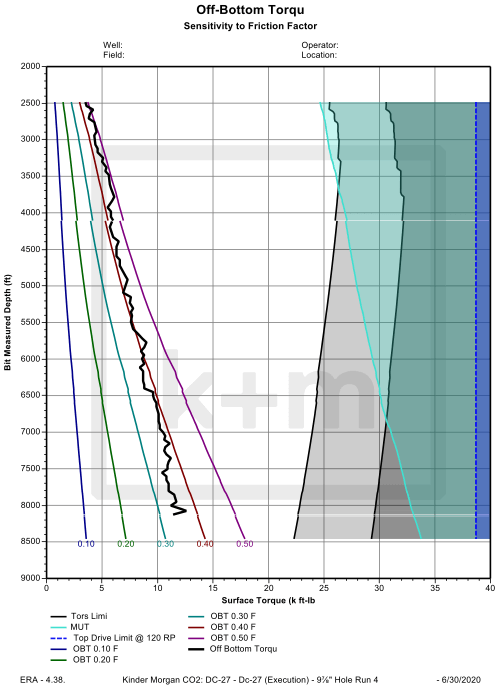
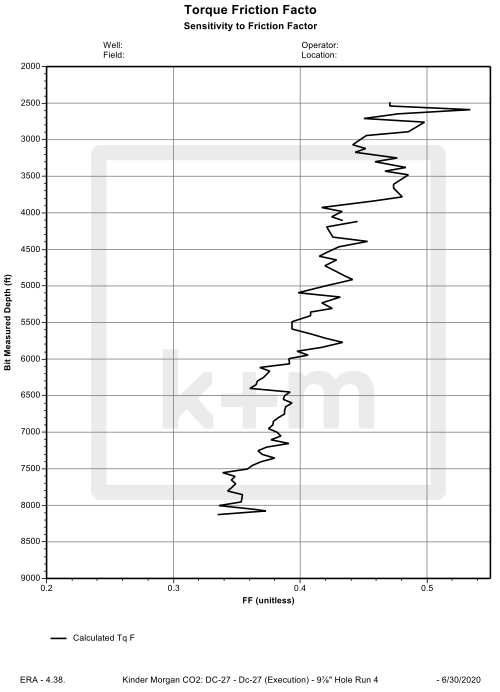