K&M Technical Engineering Services and Wellsite Support Services helped a Client toeliminate stuck pipe and hole condition incidents drilling Extreme Reach wells.
Challenge
- Drill shallow extended and extreme reach wells sidetracking from existing boreholes in a field after almost 20 years without drilling.
- Eliminate catastrophic incidents mostly related to stuck pipe, hole condition and drill string failures observed in offset wells
- Maintain an adequate drilling performance by maintaining a good weight transfer and directional control in poor consolidated sands
K&M carried out a geomechanics and a mechanical feasibility study for the wells in the field. Some of K&M recommendations as part of the study were:
- A baseline for the MPD utilization to avoid destabilizing shales in the lateral
- Specific operational parameters and practices to maintain a good hole condition and minimize fatigue of the tubulars in the curve
- A drill string configuration to balance weight transfer, ROP, ECD levels and directional control
- A two-days training to keep the entire team aligned with the ERD best practices and the K&M recommendations for the wells.
- Wellsite support to monitor the borehole behavior and adjust the practices and parameters as required by the well condition
Results
- Seven shallow Extended and Extreme Reach wells drilled successfully
- Zero catastrophic stuck pipe, hole condition or drill string failure incidents
- Drilling practices and string accessories adjusted to limit mud losses
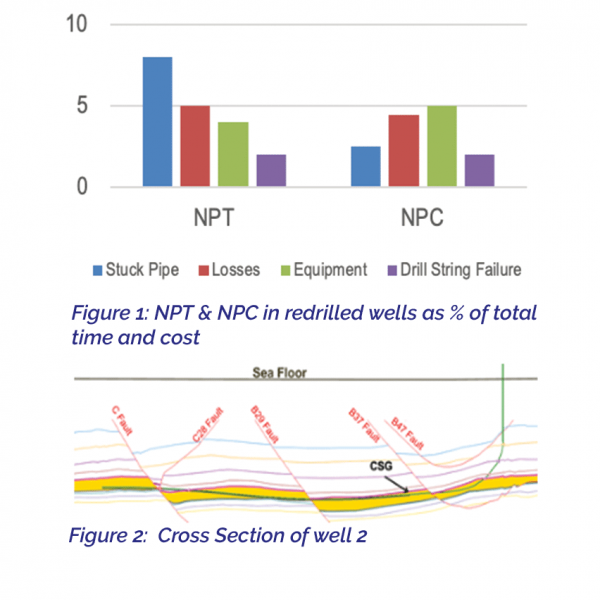
An ERD Pioneer Full Of Problems
The Clients field was discovered in 1968, between 1980 and 2001, 25 wells including Extended and Extreme Reach Wells were drilled from three different platforms.
Most of these wells were drilled over budget, with stuck pipe/hole condition, lost circulation and equipment failures (rig and downhole) as the most important Non-Productive Time (NPT) and Non-Productive Cost (NPC) categories. Particularly, the redrilled (re-entered) wells were problematics where the Stuck Pipe / Hole Condition, Circulation Losses management and Drill string Failure accounted for 15% of the total drilling time. Additionally, drilling in shallow reservoirs (less than 1,200’ TVD) had also multiple incidents of poor weight transfer and directional control in unconsolidated sands leading to multiple trips and low drilling performance.
In 2019, the client planned a campaign of seven shallow ERD wells redrilling/sidetracking from existing wells. The client planned to use MPD is required to reduce the ECD to a baseline as low as 5.5 ppg . The client contacted K&M to assist in the geomechanics, mechanical and hydraulics modeling for these wells; to help developing hole cleaning, tripping and casing runs procedures; and wellsite support while drilling these challenging wells
Designing The New Wells For Success
The new wells were planned to start opening a window in the 10¾” liner of existing wells. A curve with DLS ranging between 12.5 and 16.5°/100’ would be drilled to land the well in the reservoir at ±90°. The wells would navigate into a complex, faulted reservoir.
The Mechanical Earth Model (MEM) defined a narrow mud weight window and losses were likely using a conventional mud system. Both the ECD and Geomechanics models allowed to establish a new baseline for the MPD utilization to avoid destabilizing shales in the lateral. Several risks were identified and recommendations written for differential sticking, hole collapse when shale in encountered, losses in the sands, directional drilling problems in unconsolidated sands and open hole screens fatigue. The drill string configuration for each section was recommended to balance between weight transfer and ECD reduction.
Specific operational parameters and practices were recommended to maintain an adequate hole cleaning without jeopardizing the directional performance. Bit hydraulics optimization was discussed to maintain an optimum flow rate for hole cleaning. Connection and circulation practices were established considering the MPD equipment utilization and the presence of unconsolidated sands. Specific operational limits and practices were established to minimize fatigue of the tubulars in the curve.
A two-days training with the rig crew was delivered where in addition to the specific horizontal drilling knowledge, the K&M study conclusions and recommendation were shared and discussed.
Mission Accomplished: No Catastrophic Hole ConditionIncidents, Optimum WeightTransmission To Bottom
Six wells were drilled and completed without any catastrophic stuck pipe or hole condition incidents. Three of the wells were in the Extreme Reach region. Only one short pack off event occurred in one of the wells following a survey at the bottom of the avalanche zone. All the laterals were drilled successfully, and the screens reached bottom without incidents. Specific operational parameters and practices were established to minimize fatigue of the tubulars located in the curve. When required to rotate, the bending stresses of the screens were closely monitored to avoid string failures. The recommended drill strings allowed to transmit successfully the weight to the bit and the proposed hydraulics helped with directional control without ROP detriment. Two of the wells had to be sidetracked due to directional drilling problems.
As predicted by the Geomechanics model, no losses occurred drilling the curve of the wells targeting the sand, except for the losses result of the pack off event described before. Losses while drilling in the lateral eventually occurred as expected. Detailed observations of the nitrogen pumping, ECD behavior and resulting losses helped to refine the drilling and connection practices as well as the utilization of float valve and jet subs in the drill string to limit mud losses. Thief zones identified in the faulty environment. Cavings presence was monitored when the lateral left the sand and precaution taken to avoid pack offs. Specific practices were applied to minimize differential sticking.
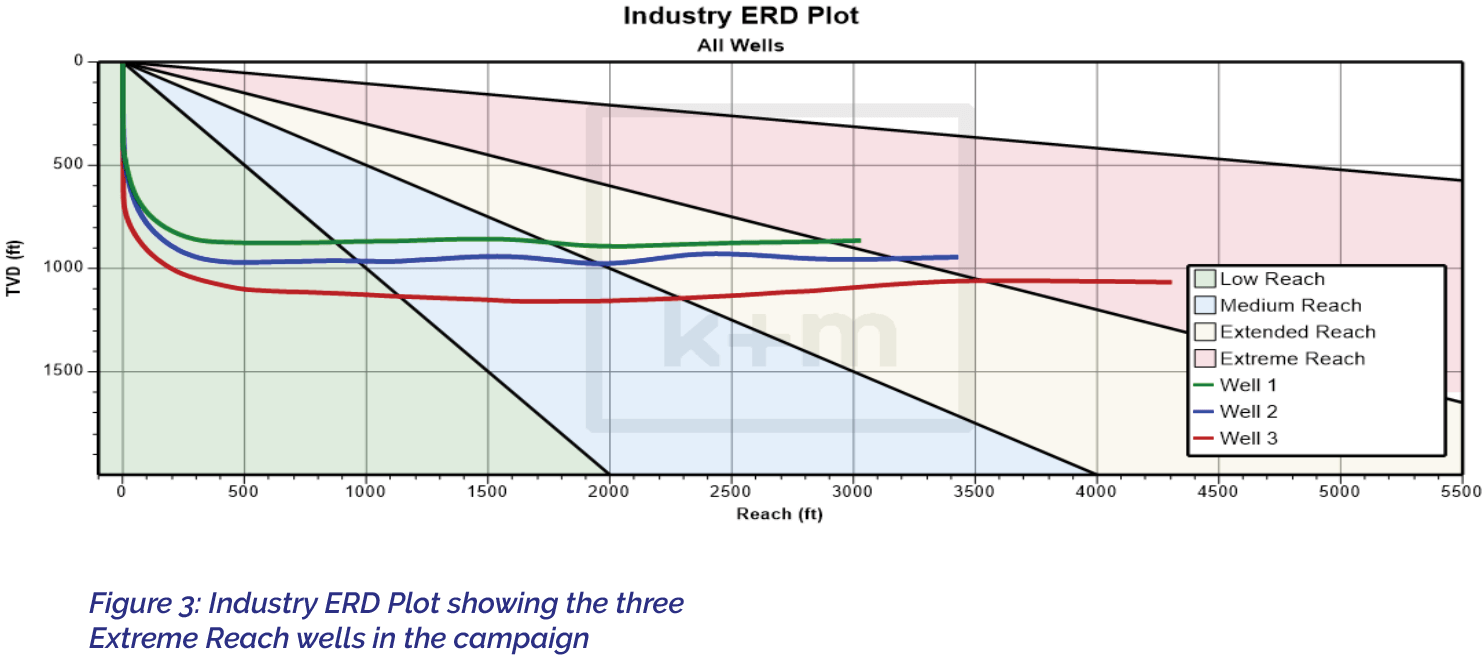