CHALLENGE
Due to logistics challenges, NAF was used for drilling the low-angle 26° section. Over the course of years, this resulted in pack-offs which in turn caused losses, bent drill pipe, and lost BHA.
SOLUTION
K&M Technology Group first implemented operations practices that prevented pack-offs from occurring, while investigating various avenues to arrive at an engineered solution. The evidence collected suggested cuttings were being generated that could not be moved out of the hole with the achievable hole cleaning parameters. Changing to a loss aggressive mill tooth bit was recommended, which would generate smaller cuttings that it was possible to clean out of the hole.
RESULTS
Using the less aggressive bit resulted in zero fill encountered after the wiper and casing run. This outcome was repeated over the following 5 wells.
A Unique Scenario Results In A Unique Challenge
Non-Aqueous Fluid (NAF) was required in the lower hole sections of the wells, and so for logistical reasons was also employed for drilling the low-angle 26″ section. Utilizing WBM for the 26″ section would have required offloading the NAF from the previous well, to
accommodate the WBM for starting the next. This additional time would inevitably be extended by weather occasionally, particularly in winter when sea-ice introduced further uncertainty.
Hole cleaning issues had been present for at least the previous 8 years. Symptoms included being unable to pick the string up from bottom without flow, and a large amount of fill encountered after wiper trips and with the casing. On average, the length of fill was ~40m, although up to 90m of fill had been observed. The large volume of fill remained present despite circulating numerous bottoms up, both before and after wiper trips.
The poor hole cleaning had led to pack-offs when bringing up flow after connection, which had resulted in losses, and had also caused the string to be displaced upwards, bending the drill pipe above the rotary table. Separately, a stuck pipe event had occurred while reaming close to bottom with low flow. There are very few cases world-wide where such large low-angle holes are drilled using NAF. The much more common WBM system permits hole cleaning via dispersion.
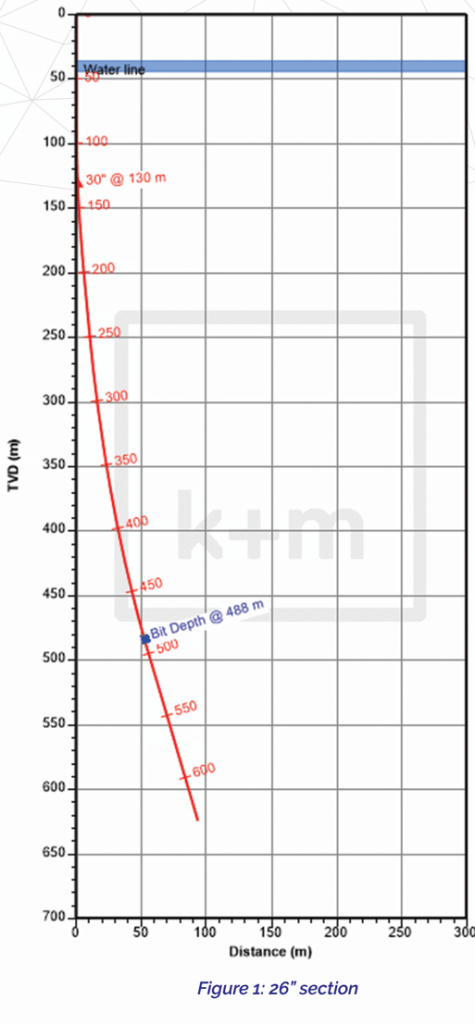
Implementing Practices To Prevent Reoccurrence, While Investigating Further
As a temporary solution to prevent reoccurrence, operational practices were implemented such as only picking up from bottom with full flow rate, and staging the pumps up after connection in consistent increments and recording the pressure at each increase to permit quick recognition of a pack-off. An engineered solution is always preferred over procedural controls, since they eliminate the human factor, and so investigation continued to find an engineered solution. Previously ROP was as high as 45 m/hr, with 4,000 lpm flow rate and mud rheology of a 6 rpm reading of ~25. Flow rate was increased to 4,600 Ipm (as limited by the surface system), the mud rheology increased to a 6 rpm of~33, and ROP limited to 25 m/hr. The combination of all these changes did not reduce the volume of fill.
Meanwhile, the implications of switching to WBM were assessed. One concern was the potential instability that the much lower inhibition would cause. K&M performed immersion testing of cuttings at the wellsite, as shown in Figure 2, which revealed considerable reactivity to water. This finding, along with the logistical challenges, strengthened the case that NAF was the preferred fluid, if a solution to the hole cleaning challenge could be found.
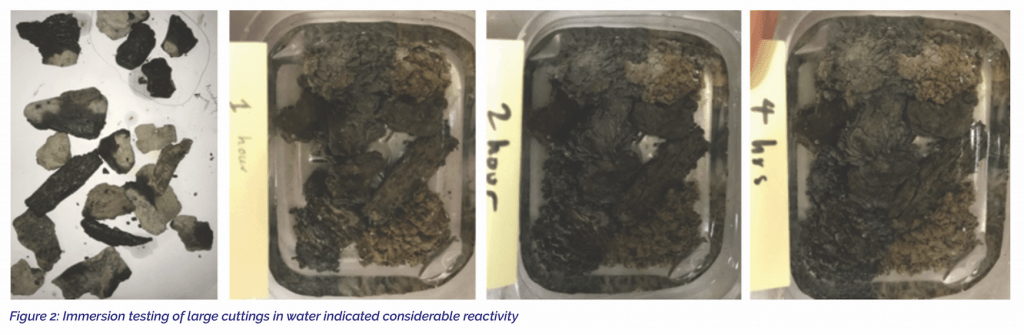
Experimenting with a variety of inputs in the low-angle hole cleaning model suggested that, if solids were very large and stayed intact, they would never be lifted out of the hole with the flow rate and rheology that could be delivered. That would remain true regardless of circulating duration. If such a phenomenon was indeed occurring, all previous observations would be explained. The following built confidence that the hole cleaning challenge was a result of cuttings so large they could not be circulated out:
- The mill tooth bit, shown in Figure 3, was very aggressive (IADC 115) with large teeth that was capable of producing very large cuttings in soft rock
- Close tracking of the maximum solids size on one well revealed that as additional cleaning capability was delivered, the maximum cutting size arriving at surface increased. A certain size was observed while drilling, with arger cuttings observed while circulating inside the conductor after backreaming out of open hole, and cuttings that were even larger (although also less spherical – the more spherical cuttings would have fallen to bottom instead of becoming suspended) observed when running casing which resulted in relatively high AV compared to circulating with the drill string
- The string was backreamed out of open hole and then pumped out to the HWDP on the same well. During this operation, ECD continuously increased, indicating increasing cuttings concentration above the PWD sensor as the higher AV across the large OD BHA was able to move the cuttings up the hole. Since it was decided to stop pumping out of hole at the HWDP, mass unloading was not observed at the shakers
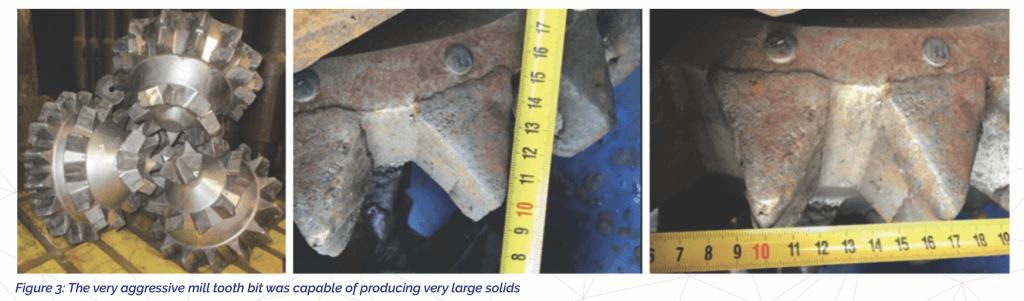
With strong evidence that cuttings existed that were too big to be lifted by even the maximum flow rate and rheology that could be delivered, reducing the size of the cuttings became the focus.
This was achieved by using a less aggressive mill tooth bit (IADC 135), with smaller cutters as shown in Figure 4. This reduced the volume of fill to zero, which was then repeated on the next 5 wells.
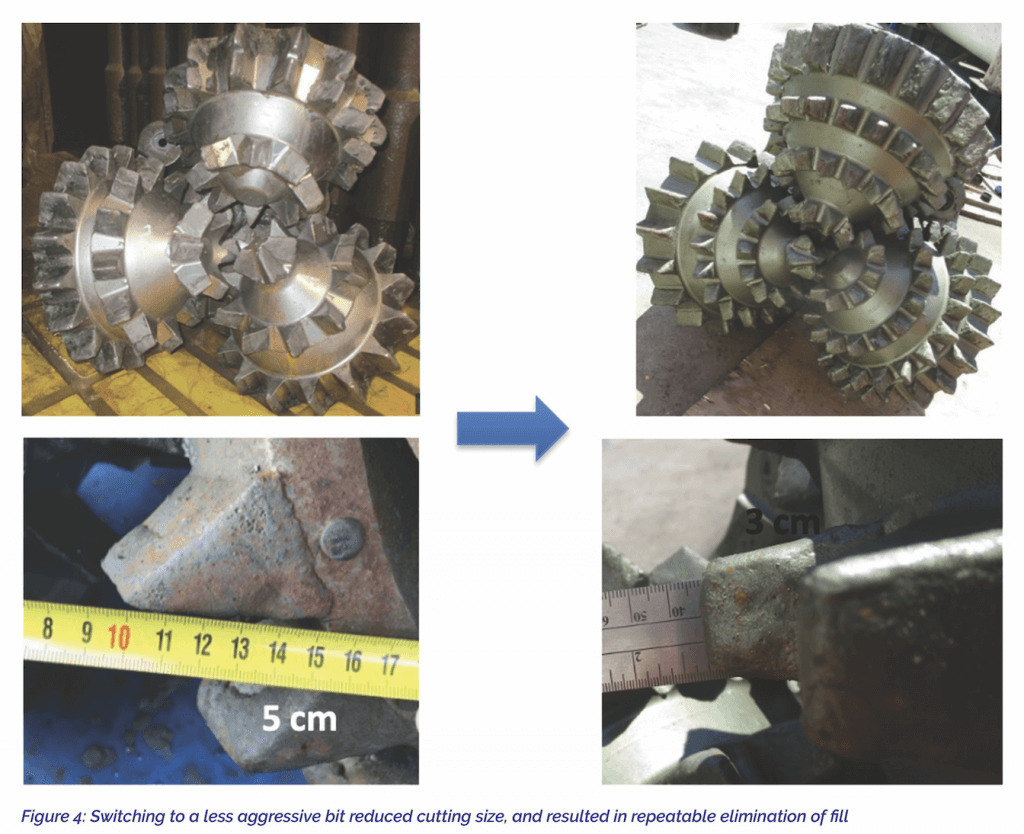